You’re managing multiple properties, juggling maintenance requests, and tracking a variety of assets—all while trying to keep everything running smoothly. Then, the HVAC system in one building goes down, a critical maintenance inspection gets missed in another, and you’re left scrambling to pick up the pieces. Sound familiar?
Without a solid system in place, facility management can turn into a fire drill, where you’re always reacting to issues rather than staying ahead of them.
That’s where facility management software comes in. It centralizes maintenance schedules, asset tracking, and work orders so you can be proactive instead of reactive. Whether you’re overseeing commercial buildings, healthcare facilities, or even a manufacturing plant, this software ensures nothing falls through the cracks.
In this post, we’re diving into what facility management software is and how it can give you more control over the bigger picture so you can save time, reduce costs, and keep your operations running smoothly.
- What is facility management software?
- Why do you need facility maintenance software?
- Key features of the best facility maintenance software
- See how Reftab makes facility management simpler
What is Facility Management Software?
Facility management software helps organizations manage their physical assets and operations more efficiently. It centralizes tasks like maintenance scheduling, asset tracking, tool check-in, and asset reporting.
Many industries, from commercial real estate and healthcare to education and manufacturing, rely on it to keep things running smoothly. And professionals like facility managers, property managers, and maintenance teams use it to streamline daily operations and improve how buildings and equipment are maintained.
Why You Need Facility Maintenance Software?
No matter the industry, facility maintenance software helps organizations be proactive rather than reactive. It’s about creating a smarter, more efficient way to manage the systems and equipment that are critical to your business. With the right software in place, you reduce the risk of unexpected breakdowns, save on repair costs, and improve overall operational efficiency.
For instance, in manufacturing, the stakes can be high. A single piece of machinery going down can halt an entire production line, leading to thousands in lost revenue for every minute it’s offline. With the right facility maintenance software, manufacturers can monitor equipment health in real-time, predict when maintenance is needed, and schedule repairs before a breakdown occurs. This kind of proactive management keeps production moving and eliminates costly downtime.
Key Features of the Best Facility Maintenance Software
When choosing facility maintenance software, you need a solution that can handle work orders, track assets, manage inventory, and provide real-time insights, all while being easy to use and adaptable to your company’s growth. Here’s what to look for:
Managing work orders
First, work order management is essential. You want a system that makes it easy to create, assign, and track work orders in real time. Automating these workflows allows teams to respond faster to maintenance needs.
For example, if a machine breaks down on a construction site, the software can automatically generate and assign a work order, so technicians can address the problem without delay. Additionally, having a smartphone app means field technicians can update work orders on the go, ensuring issues are resolved quickly, even in remote locations.
Tracking all of your assets
Asset management is another crucial feature. You need to keep track of all your equipment in one centralized system, including its maintenance history and performance data. This helps extend the lifespan of your assets and ensures they are operating efficiently.
In fact, good asset management software not only helps you know where everything is but also integrates with barcodes or RFID tags, so you can scan and update asset information in real-time. This level of tracking can prevent costly losses, especially when managing expensive equipment on multiple job sites.
Schedule maintenance and work orders
Instead of scrambling to fix an emergency issue, preventive maintenance schedules ensure your equipment gets the care it needs before something goes wrong.
It also helps extend the life of assets by ensuring regular care and upkeep, which can save you money on repairs and replacements.
A key benefit of any good facility maintenance software is preventive maintenance scheduling.
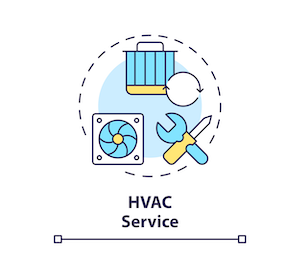
Instead of scrambling to fix an emergency issue, preventive maintenance schedules ensure your equipment gets the care it needs before something goes wrong.
It also helps extend the life of assets by ensuring regular care and upkeep, which can save you money on repairs and replacements.
For instance, if you’ve got a critical generator on a job site that, if it goes down, delays the entire project. With preventive maintenance scheduling, you’re automatically reminded when it’s time for service, based on the equipment’s actual usage. No more guesswork, and no more unexpected breakdowns.
Collect data and insights
Facility management software with advanced analytics goes beyond just telling you what’s happening. It helps you understand why it is happening.
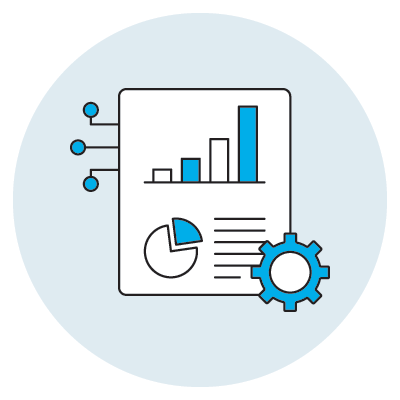
At the minimum, you should be able to pull up detailed reports on equipment usage, maintenance costs, and asset performance to make informed decisions. This can also help you identify inefficiencies and areas for improvement.
Let’s say you’re managing multiple facilities, and your HVAC systems in three buildings are constantly requiring maintenance. With advanced data, you can dig into the reasons behind these frequent breakdowns. Is it the age of the equipment? Is it being overused? Maybe it’s time for a more energy-efficient upgrade.
Access the information you need on the go
Technicians should be able to access everything they need from their phone or tablet, even in areas with limited internet access. With a mobile app, your team can update asset statuses, log maintenance tasks, and complete work orders from the field.
For instance, if a generator breaks down, your technician can immediately create a work order on their mobile device, notify the team, and get things moving without delay. It’s this kind of instant communication that keeps small issues from turning into costly problems.
Integrate with your existing tools
The software you choose should connect with your other business tools, like accounting software, ERP systems, or project management platforms. So, you can pull data from multiple sources and manage everything from one place.
If it doesn’t integrate with the tools you’re already using, it’s going to create more headaches than it solves.
Imagine tracking equipment costs in one system, maintenance schedules in another, and asset locations in yet another. It’s a recipe for confusion. With proper integration, all your data flows into one central hub.
Scalability
As your business grows, so do your facility management needs. Maybe you’re adding new locations, more equipment, or expanding your maintenance team. That’s why customization and scalability are key when choosing facility management software. You need a system that grows with you, allowing you to add new assets, locations, or users without skipping a beat.
Let’s say you’re managing facilities across five job sites, and next year, that number is set to double. You don’t want to outgrow your software. Instead, look for a platform that’s flexible enough to handle that growth.
See How Reftab Makes Facility Management Simpler
Facility management software is a necessity for keeping your operations efficient, organized, and under control. Streamlining everything from maintenance schedules to asset tracking helps you prevent costly downtime, stay ahead of issues, and ensure your buildings and equipment are always running at peak performance. Whether you’re managing multiple locations or handling complex maintenance requests, the right software allows you to be proactive, saving both time and money in the long run. Ready to take your facility asset management to the next level? Sign up for a free Reftab account.