A preventive maintenance program is key to ensuring all equipment is operating at full capacity. Your equipment’s manufacturer outlines specific tasks in order to maintain their individual piece of equipment. The hard part to this is actually completing the required maintenance on time.
You may have a dedicated spreadsheet dedicated to maintenance, a clipboard attached to the asset or even a program to help with this maintenance. All of these are completely acceptable ways to achieve the same result. No matter how you look to implement your program we have outlined an 8 step process to achieve this.
- Choose a Test Asset
- Create a Baseline
- Gather Data
- Manage Spares, Consumables and Tools
- Implement a Maintenance Management Program
- Maintenance Schedules
- Monitor and Adjust Program
- Recreate this Program for All Assets
Step 1 – Choose a Test Asset
In our experience, creating a maintenance program for one asset is much safer than trying to reinvent the wheel for your entire floor at one time. There will be bumps in the road as this process does take time to get exactly right. However, if you can perfect a program with one asset, you will very easily be able to duplicate this process ten, twenty even one hundred times over.
In order to find the right test asset, we recommend choosing one that will cost the least amount of money when down. Your first maintenance program may have unnecessary downtime while trying to find the right process. Any machine that isn’t running is time and money lost, so its best to choose an asset that can be down without crippling your workforce.
Step 2 – Create a Baseline
Once you have chosen the Test Asset you need a good baseline for where things have started. This can be anything from current performance to the current maintenance processes. If you don’t have a starting point there is no way to know which direction you are heading. A recommendation is how much unexpected downtime a particular machine has head in the past.
Step 3 – Gather Data
Each machine will have a specific maintenance schedule provided from the manufacturer. This could be anything from the amount of running hours to a set schedule. You will need to do the proper research on your Test Asset to ensure you are completing maintenance exactly as intended. Most manufacturers will void warranty if maintenance has been completed improperly.
Another great place to start is to ask; What were the reasons for downtime on this machine and what could be done to prevent the downtime? You may need to include extra tasks in your maintenance plan after finding out ways to prevent downtime.
Step 4 – Manage Spares, Consumables and Tools
This step is extremely important in knowing that you have exactly what is needed to complete the desired maintenance. Now that you know the tasks needed, ask yourself what equipment is needed to complete these tasks. Whether it is specific fluid (consumable), a specific spare, or even a tool that is needed. You need a place to track these items and a clear plan on when and how to use them. You should also have a plan on when and how to obtain more of these items when the time is right.
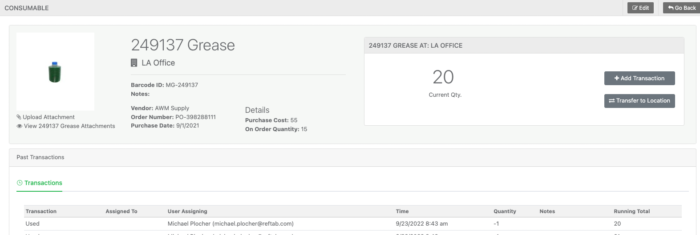
Step 5 – Implement your Maintenance Management Program
Step 5 is to decide the specific process you are going take. By choosing proper maintenance software you can be alerted when its time to order replacement consumables or even when your next preventative maintenance is due.
You should come up with the proper processes at this point. How should your technicians handle maintenance and what do you expect from them? You should have clear and defined processes for each task in order to improve accountability.
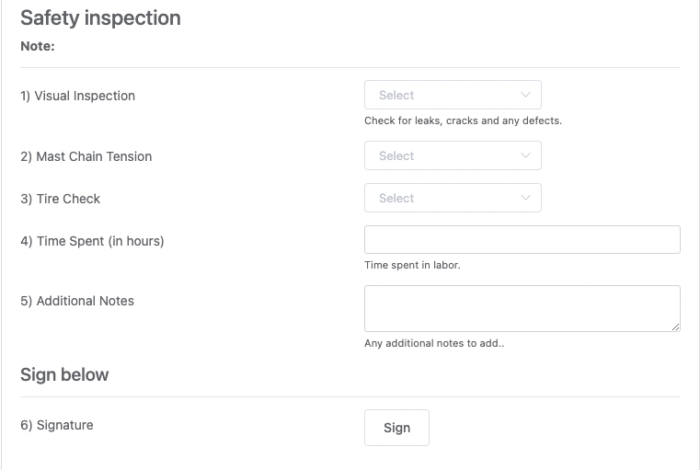
Step 6 – Maintenance Schedules
Now that your employees have clearly defined tasks in mind. We need to decide how often your maintenance should be performed. If using a maintenance management program you may be able to implement predictive maintenance based upon run time, mileage, etc. Your manufacturer will also have timelines within the specifications for each equipment. Find the tasks that should be done weekly, monthly or yearly and create the proper schedule for those.
You also need to decide how you want to stay on top of this schedule, whether you are writing it in a calendar or you want to be notified will depend on the route chosen in the previous step. The easiest way would be to have your managers notified of the maintenance. You can also choose to have them go and check the calendar themselves, this could lead to issues but it is completely up to you and the way you run your business.
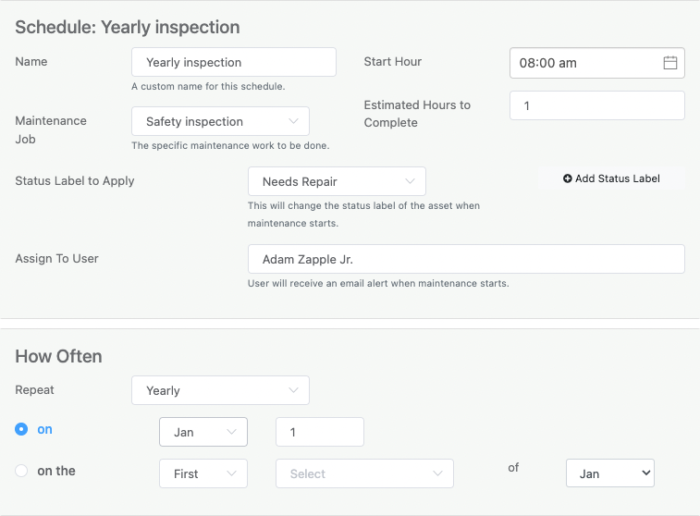
Step 7 – Monitor and Adjust Program
As mentioned in step 1, there will be bumps in the road. The process we have come up with may not be the perfect way to complete maintenance. We’re perfectionists at Reftab and believe in always adjusting your program to keep up with changes in the business. Gather your data from step 2 and run those same tests. Ask yourself the same questions to find out exactly how well the maintenance program is working. This is a good time to ask the technicians how the process is working.
The idea behind this step is to perfect maintenance on our test asset. You may need to head back to Step 6 and adjust your schedule. Or even, step 5 and completely readjust the program you implemented. Either way you choose to go this is much easier done on one asset, rather than the entire floor.
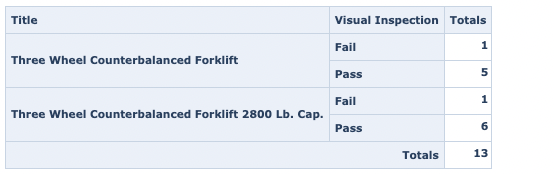
Step 8 – Recreate this Program for Each Asset
Once your Test Asset maintenance is running exactly as desired, and you believe you have reached perfection. Its time to recreate these steps on each and every asset on the floor. We recommend taking it slow still, you may run into a few bumps depending on the separate manufacturers of each asset.
Now that you have a good idea on how to implement a perfect program it will be much easier to duplicate this process. We know what went wrong the first time and we can avoid those same mistakes. You may run into more mistakes but that is exactly why we recommend taking this process slow and steady. The payoff in the longterm is much greater if you take your time and ensure this process is perfect.
Conclusion
Implementing a Maintenance Schedule is absolutely daunting at first glance. But if you follow these 8 steps listed, you should have a smooth transition into a successful maintenance program. If you need any assistance here, feel free to schedule a demo with us. We will be here every step of the way and can ensure the processes you’re coming up with will fit the needs of your business.